Since 2018, Tonasco has spearheaded the adoption of Industry 4.0 principles in Malaysia. Today, we revisit a pivotal moment when Tonasco shared its success story of integrating Digital Twin technology at the “Intelligent Manufacturing Conference 2023,” co-hosted by Messe Frankfurt (HK) Ltd and Selangor Human Resource Development Centre (SHRDC) at Kuala Lumpur Convention Centre (KLCC). During the event, Sheau-Wei Lin, Tonasco Group Managing Director, provided a comprehensive overview from a business perspective, highlighting the triggers, challenges, and lessons learned throughout our journey of building our first digital twin for a 5-axis CNC Milling Centre.
Triggers for Adopting Industry 4.0
Tonasco’s drive to embrace Industry 4.0 stemmed from several factors. Firstly, we aimed to secure higher-value jobs by serving more high-tech clients from semiconductors, optics, diagnostics and medical sectors. These clients demanded increasingly intricate component features with higher precision and higher surface finishing standards. Secondly, faced with a talent shortage within the machining industry, particularly for highly-skilled machinists for 5-axis CNC Milling Centres and Mill Turn Machines, we embarked on a quest for innovative solutions to address this challenge.
Embracing Innovation Amidst Uncertainty
In response to these challenges and new market demands, Tonasco invested in state-of-the-art 5-axis CNC machines, automation, robotics, embracing the core principles of Industry 4.0. These cutting-edge machines offer heightened complexity with multiple axes operating simultaneously at elevated speeds and power levels. This strategic initiative culminated in the unveiling of Tonasco Smart Factory Phase 1 in 2020, marking a significant milestone in our journey towards digital transformation.
However, adopting new technologies at high costs without much prior experience also meant exposing the business and operation to substantial risks. This required us to take additional measures to ensure high-yield production operation at the shopfloor and safeguard our new investments.
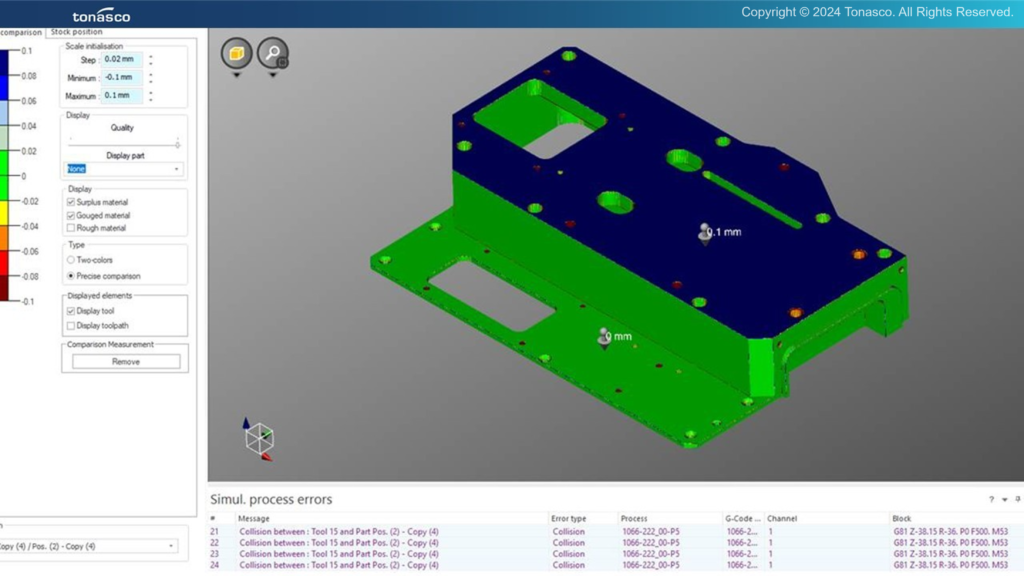
By leveraging digital twin simulation, we can verify the CAM program and simulate production processes as close to reality as possible beforehand. This allows us to troubleshoot and rectify program errors before they impact the shop floor, effectively mitigating risks and enhancing operational efficiency.
Steps in Building a Digital Twin: Makino a500Z Simultaneous 5-axis CNC Milling Centre
The construction of a Digital Twin for a 5-axis CNC Milling Centre requires several key steps. Below are the steps we felt are pivotal to our success.
Step 1. Acquire 3D Machine Models And Specifications
This foundational step in building a Digital Twin for a 5-axis CNC Milling Centre involved acquiring detailed 3D machine models and specifications from reputable vendors. These models served as the blueprint for creating an accurate digital replica of the CNC milling center. Through extensive research and collaboration with trusted technology partners, our engineering team verified that the acquired 3D models captured every intricate detail and dimension of the machine, enabling an accurate representation in the digital realm.
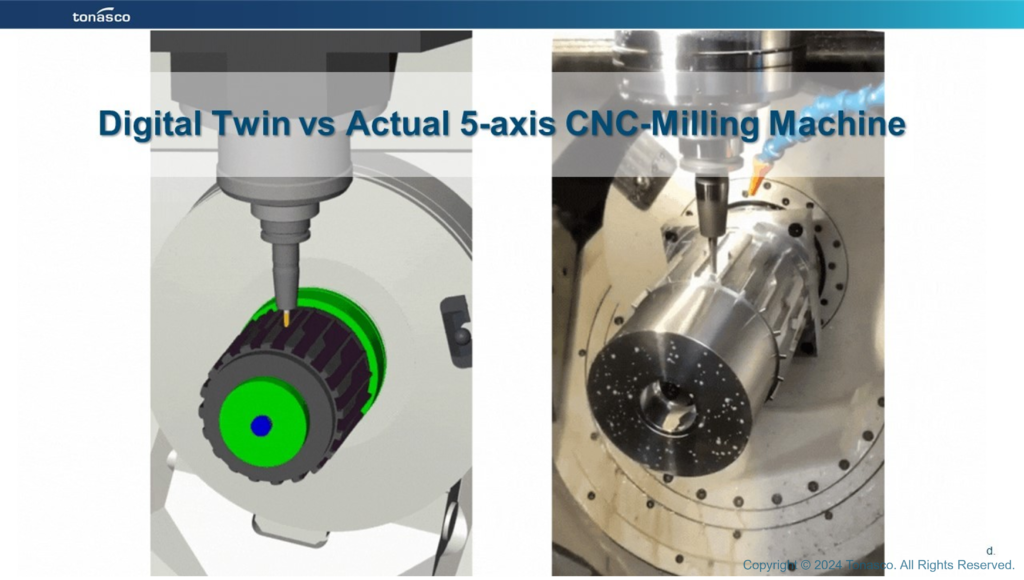
Step 2. Standardize Production Systems and Tooling
Next, the focus shifted to standardization, a critical aspect of digital twin development. This involved crafting a standardized work holding system with precise 3D representations for seamless integration. By standardizing components and processes, we bolstered the accuracy and reliability of the digital twin, laying a robust foundation for future development stages.
Step 3. Digitalise All Data Needed in the Digital Twin
With the groundwork laid for the digital twin, we proceeded to digitize all relevant data essential for its creation. This comprehensive digitalization effort included deploying a sophisticated digital tool management system, providing precise information about tools and assemblies. Leveraging cutting-edge technology and industry best practices, we ensured the system captured crucial details such as tool dimensions, materials, and performance characteristics. By digitizing this vital information, we enhanced the efficiency and effectiveness of the digital twin, empowering engineers and operators with accurate insights for optimal decision-making.
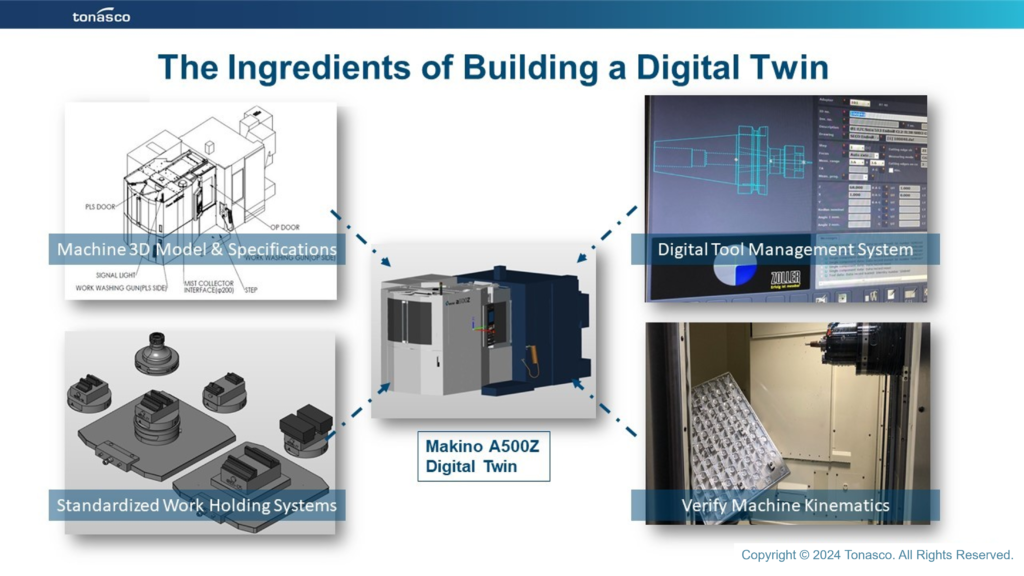
Step 4. Verify and Compare Digital Twin with Real World Machine
In the final stage, we verified and compared the digital twin with the real-world machine to ensure accuracy and reliability. This involved conducting meticulous test cuts to validate CAM postprocessors and machine kinematics. Through rigorous testing and advanced simulation, we meticulously compared the digital twin’s behavior with that of the actual machine, identifying any discrepancies. By iteratively refining based on real-world observations, we enhanced its fidelity and predictive capabilities, empowering operators with a powerful tool for optimizing production and driving continuous improvement.”
Through meticulous adherence to these steps and leveraging cutting-edge digital twin technology, Tonasco attains unmatched accuracy and reliability in its 5-axis CNC Milling Centre’s digital twin. This commitment to excellence and innovation sets new benchmarks in precision engineering and manufacturing digitalization.
Conclusion: Business Value of Digital Twin Integration for Tonasco
Investing in digital twin simulation technology conferred numerous benefits upon Tonasco, including
- Risk reduction by minimizing machine crashes, productivity losses, and delays.
- Enhanced capabilities enable smarter production of complex components.
- Improved quality with half of the quality control process completed before production.
- Mitigation of talent crisis by reducing dependency on senior staff and eliminating the need for night shifts.
With deep gratitude, we extend our thanks to our esteemed partners ZOLLER Southeast Asia , Makino Asia Group, NCSIMUL and OPEN MIND Technologies AG for their unwavering support throughout our Digital Twin journey, with whom we shall continue to explore the boundless opportunities that digital twin technology offers our manufacturing operations at Tonasco. Stay tuned for further updates as we persist in our quest to innovate and redefine precision engineering standards.