Carbon Steel Components for Semiconductor Applications
The components showcased below are tailored for semiconductor applications. These intricate components feature high-precision 2mm groove ribs, demanding a meticulous approach to machining. The precision requirements in semiconductor applications necessitate a careful balance between accuracy and efficiency throughout the machining process.
Machining Challenges & Solutions
Carbon steel components present unique challenges in machining due to their hardness in comparison to softer materials like aluminum. This necessitates the use of specialized cutting tools and strategies tailored to the specific properties of carbon steel. In this article, we delve into the precision machining of carbon steel components designed for semiconductor applications, where the focus is on achieving exacting measurements and high-quality finishes.
Unlike softer materials, carbon steel demands a distinct approach to machining. The hardness of carbon steel requires specialized cutting tools and strategies to ensure optimal results. In our machining processes, we employ unique tools designed specifically for carbon steel components. These tools are crucial for overcoming the challenges posed by the hardness of the material and ensuring precision in the final product.
Specialized Tools and Cutting Strategies
To meet the stringent requirements of machining carbon steel components, we utilize specialized tools and equipment. The component dimension measurements are 16mm (w) x 12mm (h) x 12mm (d).
The key tools involved include a 21.7mm (w) x 1.5mm (h) mini disc grooving T-slot insert cutter and a 12mm cylindrical connection type shank tool holder. These tools are chosen for their ability to handle the hardness of carbon steel while maintaining the precision required for semiconductor applications.
The machining process involves a carefully planned toolpath, with two passes each for roughing and finishing. This approach ensures that the carbon steel components undergo a systematic and controlled shaping process. To enhance stability and precision, a high-precision jig is employed during machining. This jig plays a critical role in maintaining the integrity of the components and achieving tolerances of greater than 10 microns.
Advantages of Our Strategies
Our unique cutting tools and machining strategies offer several advantages when working with carbon steel components. The specialized tools ensure efficient material removal while maintaining the required precision. The two-pass approach in the toolpath balances the need for speed in roughing with the precision demanded in finishing. Additionally, the use of a high-precision jig contributes to the overall stability of the machining process, resulting in components that meet or exceed the specified tolerances.
Precision machining of carbon steel components for semiconductor applications requires a specialized approach to overcome the challenges posed by the hardness of the material. By employing unique cutting tools, strategic machining processes, and high-precision jigs, we ensure that the final components meet the stringent requirements of the semiconductor industry. Our commitment to precision and innovation sets us apart in delivering high-quality carbon steel components for diverse applications in the semiconductor field.
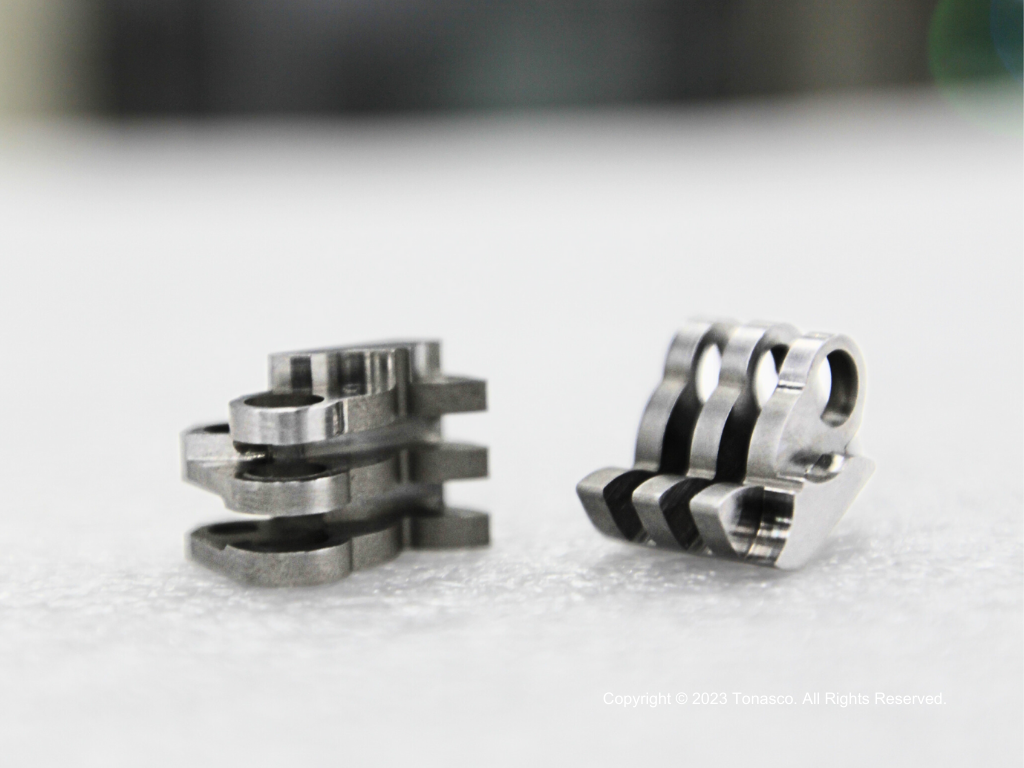
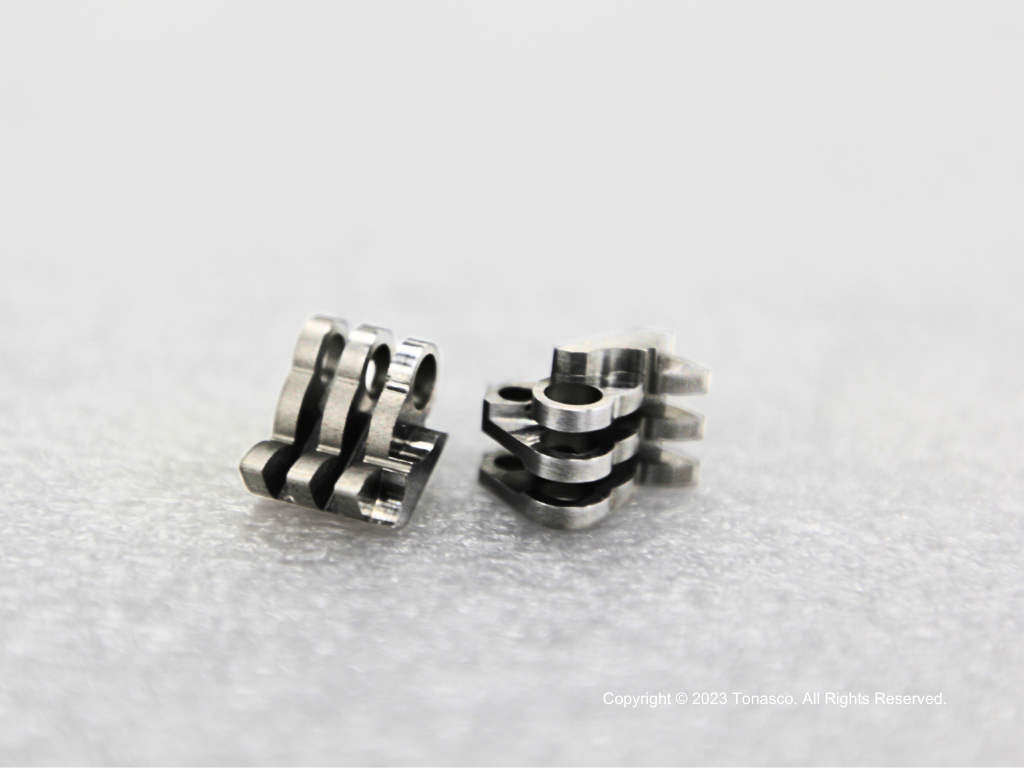
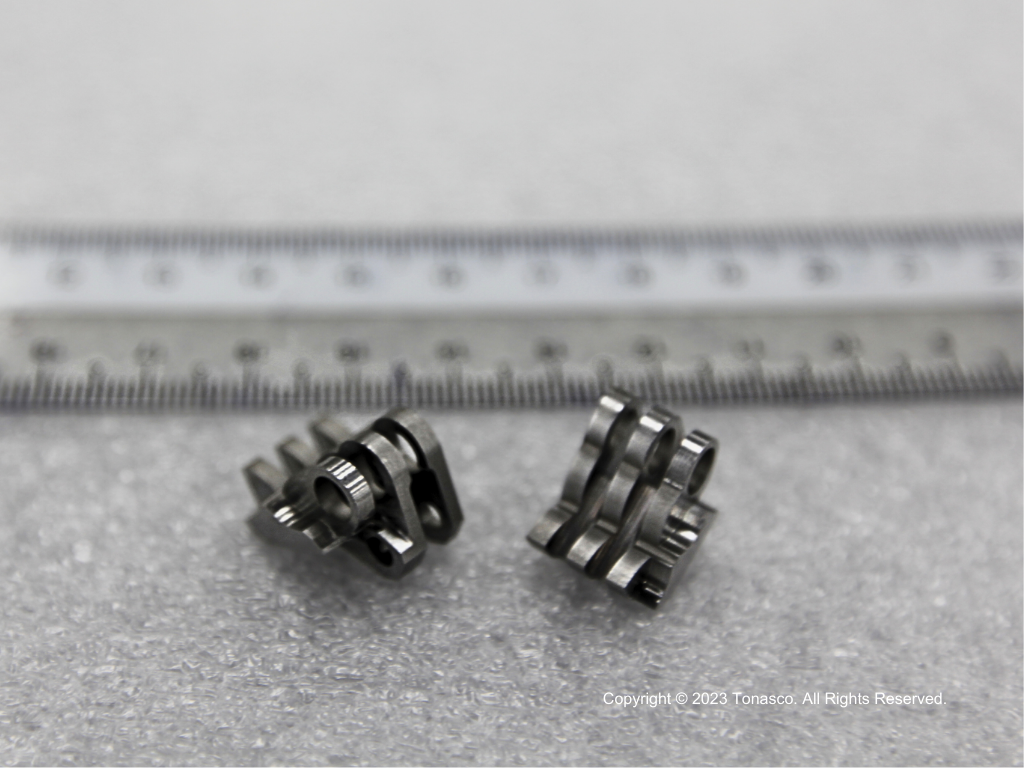